The battery enclosure is a central component of a battery-electric vehicle. Welding its various parts presents specific challenges for the welding technology used. Scansonic now offers the ALO4 series of laser welding optics, providing suitable solutions for each of these tasks. Combined with available laser beam sources and a wire feeder, a comprehensive system for laser beam welding in this crucial application area is now available.
Even though the automotive industry is currently undergoing structural changes, it is certain that the future of passenger cars will be battery-electric. The exact timeline for this transformation remains open, but all manufacturers are already consistently aligning their model ranges towards electromobility. This shift has far-reaching implications for manufacturing: while traditional areas such as engine and transmission production are losing importance, new requirements are coming into focus. One of the central challenges is establishing suitable manufacturing technologies for series production. The production of the battery enclosure is particularly in the spotlight, considering the classic parameters of industrial mass production: cycle time, quality, and cost.
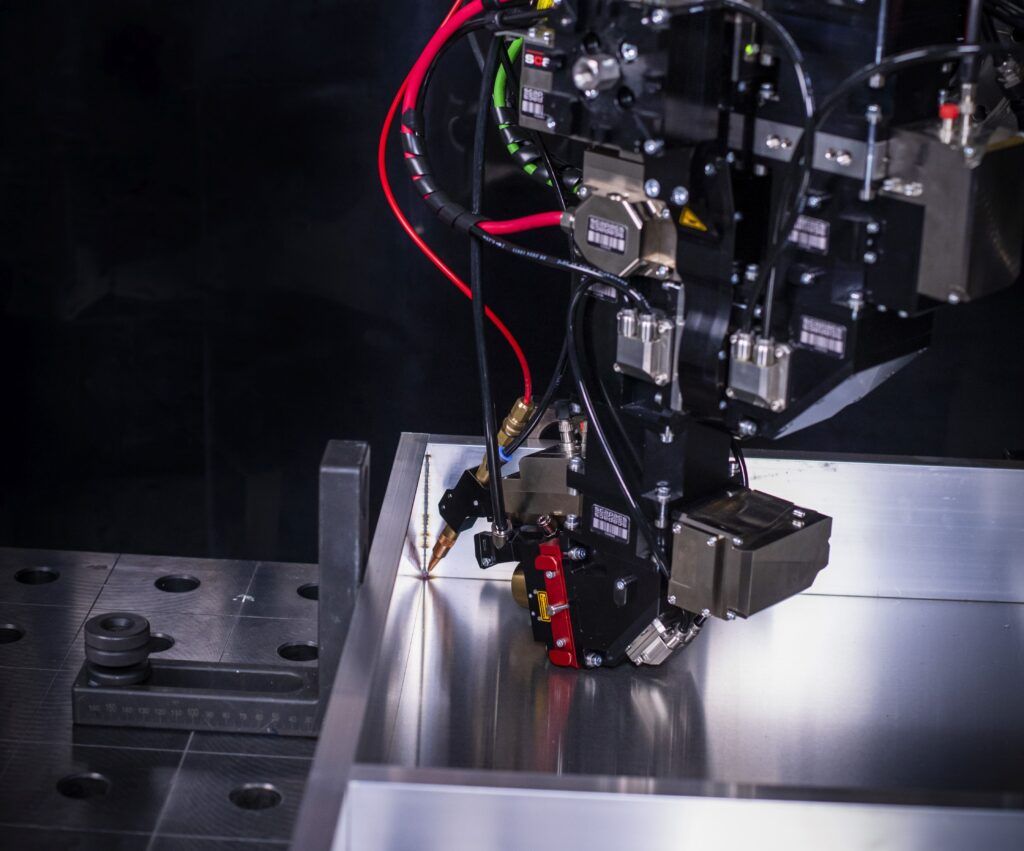
Complex Battery Enclosures
The lithium-ion batteries used in electric vehicles are mechanically sensitive and must be reliably protected against impacts, high temperatures, and moisture. Accordingly, high demands are placed on the battery enclosure: it must be sealed, have high rigidity, and include structures for cooling the cells. At the same time, low weight and economical manufacturing costs are essential. In most vehicle concepts, the battery pack is integrated into the vehicle floor, lowering the center of gravity and increasing passive protection in the event of an accident.
In series production, most OEMs rely on battery enclosures made of aluminum. The lower weight compared to steel has a direct positive impact on range. Aluminum-magnesium-silicon alloys of the 6000 series are often used, as they offer a good weight-to-strength ratio. However, a particular challenge arises from their increased tendency to form hot cracks – an aspect that places special demands on the welding process.
In addition to the material, the geometry of the battery enclosure also places high demands: different types of weld seams such as fillet welds, butt welds, and T-joints must be reproducibly joined with high quality. Overlap joints can have gaps due to manufacturing tolerances that must be reliably bridged during the welding process.
Challenges of Laser Welding
For the weld seams required in the battery enclosure, laser welding offers decisive advantages over conventional methods. It allows high processing speeds with precise energy input – depending on the application, the welding speed can be about twice as high as arc welding. The low heat input also significantly reduces the risk of deformation of the component during the joining process.
Despite these advantages, many manufacturers have so far hesitated to use laser technology consistently, as suitable optics were not available for all joining points. A combination of laser and arc welding within the same production facility often seems impractical for mass production.
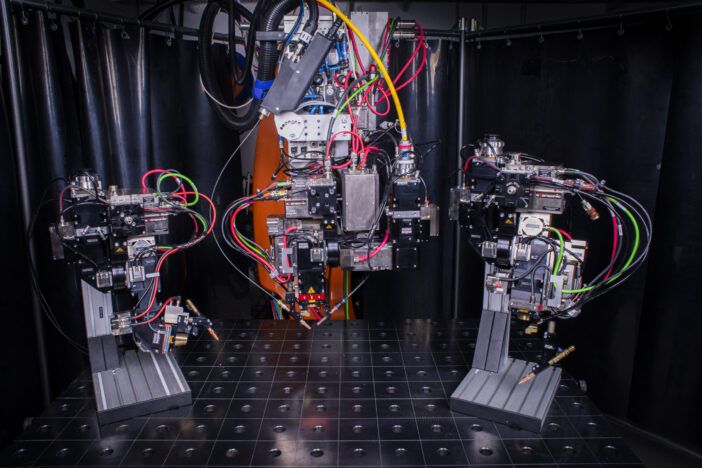
Suitable Laser Welding Optics for All Requirements
Scansonic, a leading manufacturer of laser processing optics for 25 years, has specifically developed its established ALO4 to meet the requirements in the battery enclosure sector. The resulting family of processing optics now covers all welding tasks in this area. An additional wire is used in the process. This not only reinforces the seam but also ensures, with the so-called tactile seam tracking, that the processing always takes place exactly at the edge of the component.
Especially for hot-crack-prone aluminum alloys of the 6000 series, the additional wire offers an effective approach to process stabilization, particularly regarding the formation of hot cracks. Gaps up to one-third of the thickness of the upper component can be reliably closed – the resulting weld seams are stable and crack-free.
Even larger tolerances can be bridged if the optic is additionally equipped with beam oscillation. In developing the ALO4-O, the engineers utilized existing know-how for both tactile and remote welding processes. The ALO4-O combines tactile seam tracking with the laser beam oscillation of a remote optic. Two synchronized scanner axes enable oscillations of the laser beam up to 1,000 Hz. Oscillation shape, amplitude, and frequency are freely programmable. The process can be designed so that material from the upper component is melted and used together with the additional wire for gap filling – tolerances up to 50 percent of the material thickness can be compensated. The beam oscillation also offers significant advantages for processing thicker sheets, such as the battery enclosure lid, as it achieves a wide seam connection with a smaller laser beam focus. This means less heat input compared to a larger spot without oscillation.
Adjustments for Geometrically Demanding Joints
Some weld seams must be made inside the battery enclosure – with correspondingly limited accessibility for the tool. The ALO4-L laser welding optic was developed for these applications. Its extended telescopic arm allows deeper penetration into the battery enclosure; the working distance is about 70 mm greater than the other variants of the ALO4 family.
For vertical seams inside, the series was also expanded with the ALO4-F. This optic uses a third deflection mirror that deflects the beam by 115°. This allows the vertical seams in the corners of the battery enclosure to be reliably reached and welded.
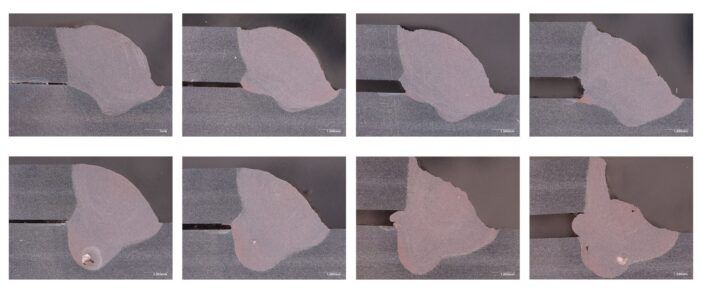
A Consistently Coordinated Complete System
The coordinated use of the four ALO4 variants brings significant advantages for production. The common control system automatically recognizes which ALO4 optic is connected and adjusts the parameters accordingly. Maintenance and spare parts inventory are also simplified by systematic standardization.
The processing optics are compatible with all common laser sources on the market. For even easier integration, Scansonic offers all other system components in combination – including the wire feeder from Dinse and suitable laser sources from Brightlight Laser Systems – from a single source. The result is an optimally coordinated complete system with high process reliability.
All variants of the ALO4 series are available with the SCeye process monitoring system developed by Scansonic. This fully documents the welding process. AI-based algorithms detect pores and spatter that escape from the melt pool. Additionally, all relevant machine and process parameters are continuously monitored – an important basis for seamless quality assurance in series production.
Scansonic is presenting the ALO4 family together with other solutions at the Battery Show Europe (3 – 5 July 2025, Stuttgart – Hall 4, A10)